ENDOTRACHEAL TUBES: INNOVATION MEETS AUTOMATION
Rotary indexing system for more productivity in endotracheal tubes production with the same quality
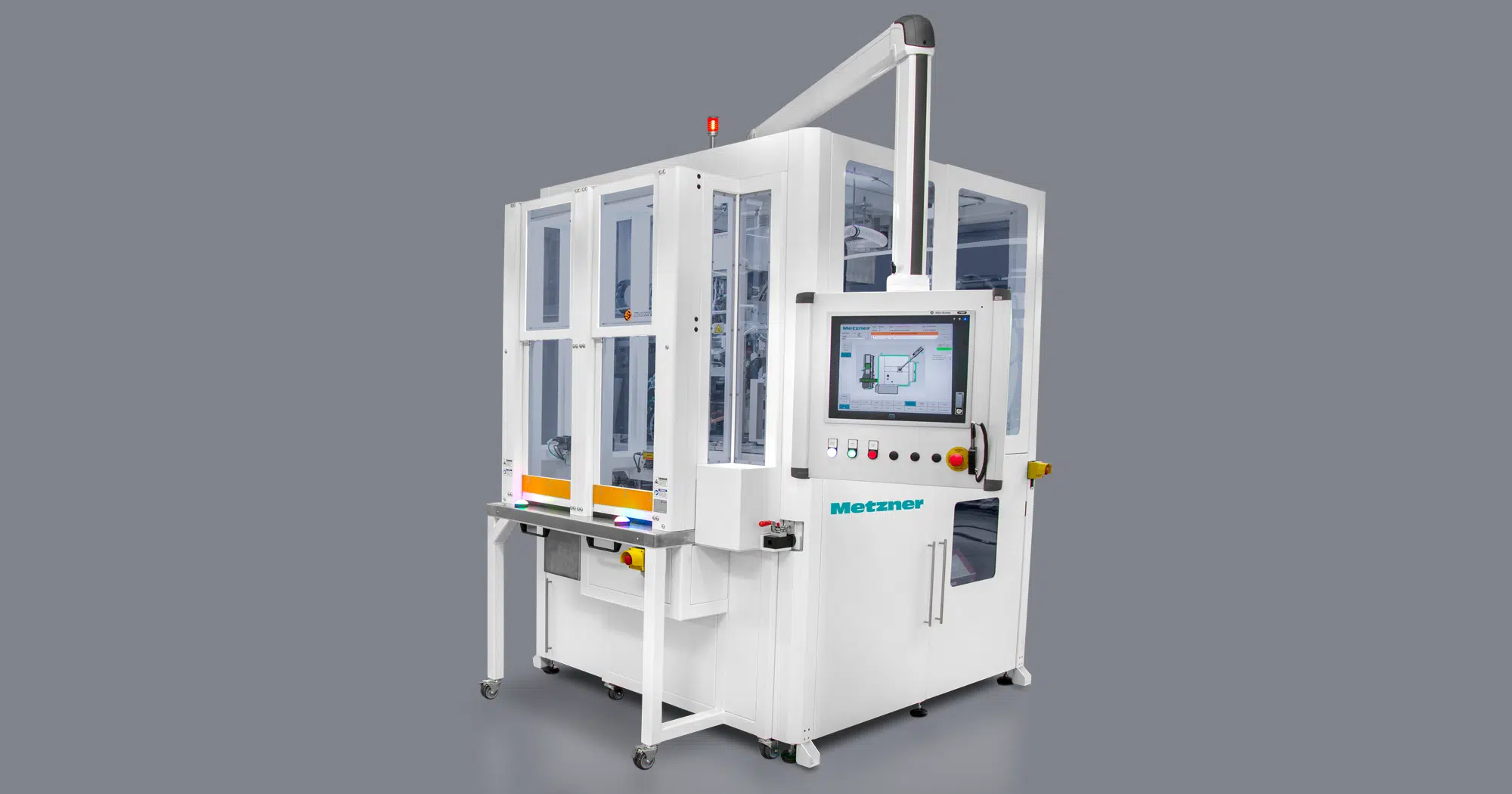
An internationally active medical technology company wanted more productivity in endotracheal tube production. The quality of the products also needed to remain the same.
Initial situation of the endotracheal tubes production
In the manufacture of reinforced endotracheal tubes, a cuff is glued. This is an inflatable cuff made of plastic or rubber, which is located at the end of a ventilation tube. This seals the tube airtight to the trachea.
However, fitting these cuffs used to be laborious manual work. Alcohol was used to clean the cuffs. This exposed the employees to harmful substances on a daily basis. It was also not possible to guarantee consistent product quality, as each employee glued the cuffs differently. The training of new employees was also very time-consuming, as it takes years of experience to master this technique.
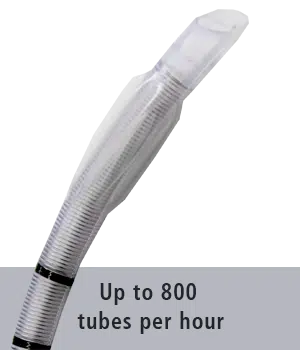
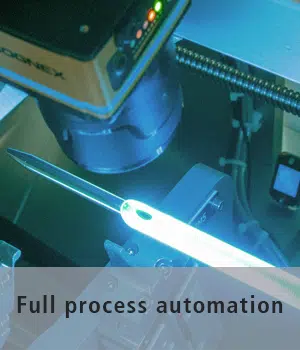
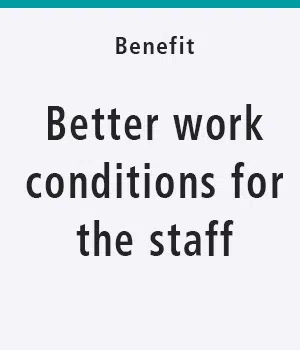
Solution through automation and the development of new technology
Automation of the existing process combined with the integration of a new technology. To meet this requirement, Metzner designed a fully automated rotary indexing system for greater productivity in the production of endotracheal tubes.
The cuff, which was previously glued by hand, is mechanically attached to the ventilation tube using welding technology. The system seals the cuff mechanically using a roller.
So, the system produces 21 different versions of the tube. 7 different sizes, each in 3 different versions. With an output of 800 tubes produced per hour, the Metzner automation offers an outstanding cycle time with consistent, high-quality results.
Ease of use and productivity in one
The customer’s objective was to fully utilize the workforce and at the same time produce a high number of tubes. The system runs through five stations in a rotary cycle. This has the advantage that neither the operator nor the machine have downtimes or waiting times. This is the only way the system can meet the cycle times of 800 tubes produced per hour.
Station 1 and 2 in alternation: The operator inserts the tube to be processed in the first step and the cuff in the next, while the machine starts production. In this way, the system works in parallel with the operator.
Station 3: The pressure rings are applied accurately. While the system waits for a drying time, it measures and checks in parallel.
Station 4: Both ends are welded at the same time. The tube now dries for a few seconds.
Station 5: The system ejects the tube.
High quality requirements
The system uses special sensors to control and monitor the insertion process. However, if the operator accidentally inserts the wrong tube or cuff, the machine stops. This prevents the machine from wasting material or damaging the system.
These high requirements and regulations that are common in the medical industry were one of the challenges for the entire Metzner design team. The end result, however, is more than satisfactory. That’s why the customer is going into series production with the system. Automation and operator-independent quality are combined with newly developed processes for welding the cuff. After a successful test phase, the feedback is a very reliable end result. The customer has also put 2 of these systems into operation.
Applications
Fully automated production line for endotrochial tubes:
- Consistent, high-quality results
- Quality control and monitoring using a vision system
- User-friendly rotary indexing system with an output of up to 800 reinforced endotracheal tubes per hour
- Processing of 7 different hoses, each with 3 different designs, in just one machine
- Machine runs parallel to the operator – no waiting times for the operator and no machine downtime
- No danger from harmful substances thanks to the development of innovative, automated welding technology
Your Individual solution
When it comes to the production of tubes, pipettes, catheters and similar products for medical technology, Metzner has a solution. How can we help you to further improve your product quality and save process costs at the same time? Challenge us: