SOLUTION FOR RUBBER + PLASTIC EXTRUSION COMPANIES
Metzner CCM 2 circular knife machine: the fast and exact way of cutting reinforced hoses
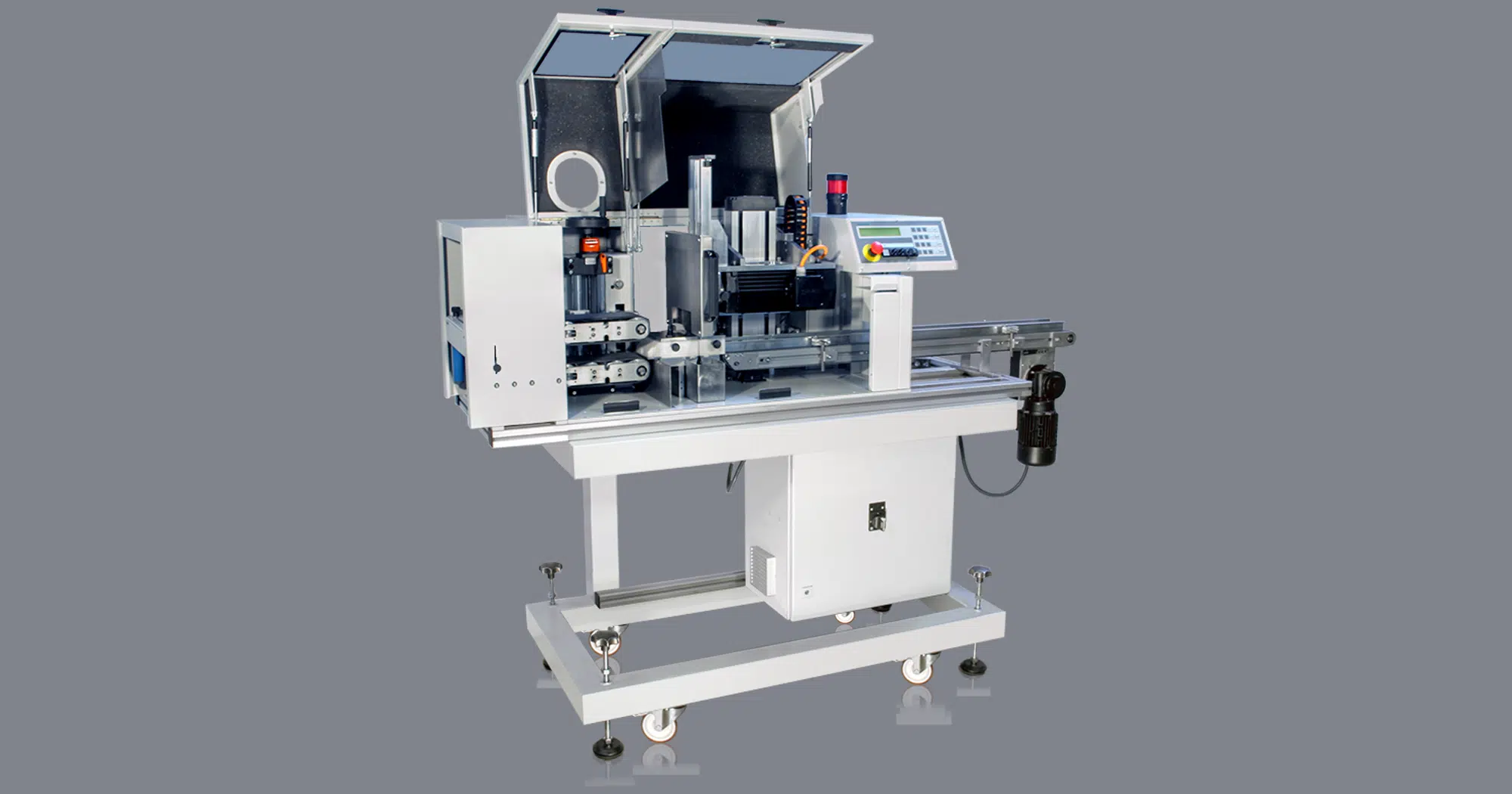
and burr formation is close to zero
for dry cuts
thanks to the long take-off belt (1,300 mm | 4'3")
The Metzner CCM 2 is made for cutting reinforced hoses, tubes and profiles. Thanks to its speed it is an ideal solution for rubber and plastic extrusion companies.
As a standard, this dry cutting machine is equipped with a dust extraction. What’s more, also an integrated take-off belt with a length of 1,300 mm | 4’3″ makes work with this machine easier.
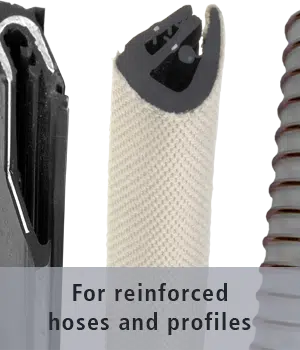
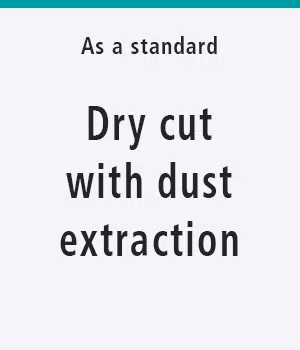
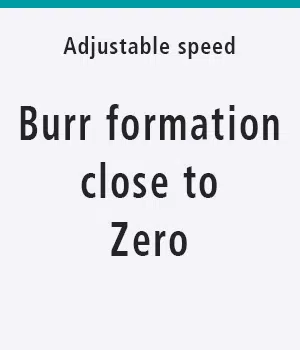
CUSTOMIZATION
As with all Metzner machines, it is possible not only to customize the CCM models, but also to adapt them to your needs with standardized modules.
Gap detection
Thanks to the gap detection, the knife cuts exactly in the gap und thus produces a snagfree cut in the metal carrier. This improves the cut, and it spares the knife.
Profile clamping
Thanks to the profile clamping, the material is optimally fixed during the cut. Another advantage occurs when you use abrasive discs. This improves the cut surfaces. Thus, they are perfectly prepared for welding the sealing profiles without reworking.
Cutting on the marks
A sensor detects marked areas and controls the cut to the mark. Of course, a required distance to the marker can be set when cutting reinforced hoses.
Automatic scrap cut
A sensor detects marked and nonconforming material areas. The machine independently performs a waste cut. Material that does not meet the specification is thus not processed further as part of the automatic quality control.
Network
With this tool, CCM machines send production status information to an external control station. Combined with Profibus connectors, they can be completely remote controlled.
E-Service Modul
Thanks to this tool, each CCM has optionally its own IP address or access to the mobile network. This is how Metzner Service supports you effectively and cost-efficiently with fault diagnoses, spare parts advice or repair recommendations.
TECHNICAL DATA
Performance data | Metzner CCM 2 |
Material dimension (depending on the selected configuration) | 100 mm x 30 mm | 3.9″ x 1.2″ |
Circular knife rotation speed | 2,000 to 3,000 or 4,000 to 10,000 |
Circular knife penetration speed max. | 30 m/min. | 98’5″/min. |
Size increments | 0.1 mm | 0.002″ |
Feeding speed | 120 m/min. | 393’8″ |
Max. cutting rate: circular knife cut | 120 cuts/min. |
Max. cutting rate: die cut | 170 cuts/min. |
Typically repeatable exactness | +/- (1 mm | 0.04″ + 0.2% L) |
Technical data | |
Electrical connection | 3~400 v; 50/60 Hz; 16 A or transformator |
Compressed air connection (only necessary with die cut) | 6 bar | 87 PSI |
Dimensions (L x W x H) | 2,060 mm x 750 mm x 1,680 mm | 7’9″ x 2’6″ x 5’6″ |
Weight | 400 kg | 882 lbs |
Eqipment | |
Control | S7 |
Gap detection | – |
Additional cutting tool | option |
Cooling water circulation | – |
Length measuring system | option |
Cutting based on marking | |
Automatic scrap cut | option |
E-service module | option |
Minimum quantity lubrication | option |